Description
Brittle fracture is the sudden or rapid fracture of a component under stress, but without undergoing any appreciable permanent deformation or ductility. The term ‘Brittle’ may be considered as one end of a scale, with ‘Ductile Fracture'1 being at the other end.
Brittle fracture is generally expected in very hard materials such as ceramics, glasses, some polymers, and metals. The pieces of a material or component that have fractured in a brittle way can often be placed back together with no appreciable change in the original dimensions or form.
Generally, once a brittle fracture is initiated it will propagate rapidly through the material until it meets a free surface (an edge) typically causing the component to collapse into two or more pieces.
Mechanism
To understand the mechanisms of brittle fracture it is useful to consider the atomic structure of a metal. Metals are made up of crystals, normally called grains, which consist of ordered layers of atoms. When metal is cold-worked, slip in atomic planes occurs causing errors in the atom stacking, known as dislocations. These dislocations can ‘pile up’, and make the metal less able to deform, increasing the hardness (termed ‘work hardening’) and making the metal more brittle. This is why some metals are annealed from time to time as they are cold-worked, allowing atoms to reorganise and dislocations to heal, softening the metal. Alternatively, some metals are worked whilst ‘hot’ or at temperatures high enough to allow the dislocations to reorganise, dissipate, and hence be eliminated.
The restriction of dislocation movement due to high dislocation densities, restrictions on their movement, or in materials with limited slip systems, can allow stresses to rise to the critical levels needed to initiate a crack. In ‘pure’ brittle fracture, cracking occurs by cleavage along specific planes of atoms within a grain. However, pure cleavage is not generally observed in the metal alloys commonly used in engineering, which may exhibit quasi-cleavage (a combination of cleavage and microvoid coalescence; a feature of ductile fracture) or some level of micro-ductility only observed at high magnification.
Anything that limits slip will make a material more brittle such as the high dislocation densities that can occur at grain boundaries, defects within the grains, but also microstructural precipitates. The composition of a metal may be selected to deliberately produce precipitates within the structure to produce such dislocation locking to engineer specific hardness and mechanical properties.
There are a number of factors that can cause, or contribute to a brittle fracture, including 1) high residual or applied stress, 2) low fracture toughness, 3) the presence of a crack-like flaw or defect within the material, 4) reduced grain size, 5) low temperatures, 6) high strain rates, 7) section size, 8) microstructure.
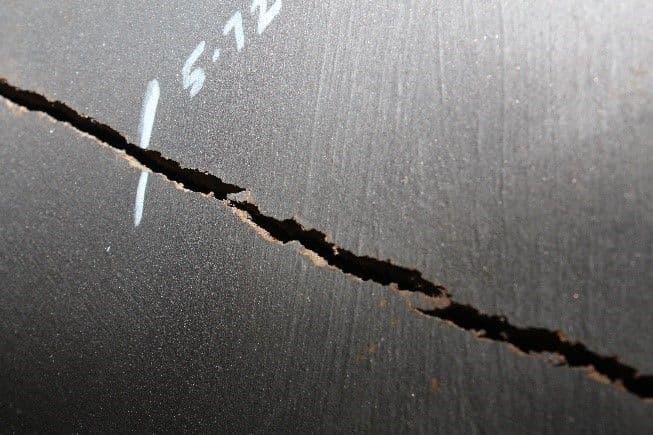
- Residual stress is that which is inherent in the material, often as a consequence of manufacturing processes. These may be produced from processes such as heat treatments, welding, and cold working where the stresses result from deformation or strains within the material. The image below shows a crack in a cast iron housing that fractured during machining. The opening of the crack and lateral displacement indicated high residual stress that remained in the material from the casting process. Applied stresses are those that are caused by external loading on the component as part of its use or operation in service.
- Low fracture toughness means that a material does not require a significant amount of energy to fail by fracture.
- Crack-like flaws or notches act as a point of stress concentration and some materials may be prone to brittle fracture in their presence, and this effect may be referred to as ‘notch sensitivity’ i.e. the material may be prone to brittle fracture in the presence of a notch.
- As grains get smaller in a material, the fracture becomes more brittle. This is because in smaller grains, dislocations have less distance to move before they encounter a grain boundary and are halted. When dislocations cannot move very far, plastic deformation before fracture decreases, and so the material's fracture mode is more brittle.
- Another key element that can cause brittle fracture is temperature. At lower temperatures atom vibration decreases, and movement of atoms and dislocations is restricted, causing an increase in the material’s propensity to brittle behaviour.
- The rate at which a material is loaded and subsequently deformed can affect the manner in which it subsequently fractures. At very high strain rates, such as that experienced in impact, strain rates may be so high that a normally ductile material may fail in a brittle manner.
- The section size or thickness of a material subjected to loading to cause fracture will affect how the fracture propagates. When subjected to loading, a material will be subjected to deformation in three perpendicular axes. For example, in a tensile test on a square-sectioned bar, the material will elongate in the direction that the load is applied. But in the other two directions, the sides of the bar will deform and narrow; the Poisson effect. In a material under load, which is narrow, this deformation may extend for the full thickness of the sample and it is said to behave in a ductile manner. With increasing sectional size (thickness) the depth to which this deformation extends stays relatively constant, and the material in the ‘depth’ of the sample does not deform as it is restrained in all directions by the surrounding material. The resulting fracture will exhibit small lips of deformed material around the edges that formed the original surfaces of the sample (sometimes referred to as shear lips; a ductile fracture). However, in the central section of the component, the fracture may exhibit typical brittle fracture characteristics often appearing as a flat fracture surface orientated perpendicular to the direction of loading.
- Iron alloys (e.g. steel) may transform to martensite if given a sufficiently rapid quench from high temperatures. Martensite is a metastable phase and in steel, consists of a supersaturated solution of carbon in iron. Due to the high lattice distortion resulting from the rapid quench, martensite exhibits high residual stress. This induces high hardness and strength to the steel although a corresponding increase in brittleness.
Appearance
Fractures that occur in service (i.e. not under controlled laboratory tests) may not necessarily exhibit just brittle or ductile characteristics, but may exhibit elements of both fracture modes. At low magnification, or just by ‘eye’, a fracture may appear to be brittle, but at higher magnifications ductile fracture modes and characteristics may be observed. However, the general characteristics are often sufficient for the classification of the mode of fracture and for brittle fracture, as described above, can be summarised as a fracture that occurs without any appreciable permanent deformation.
Occasionally, brittle fractures may exhibit features called ‘river marks’. These typically manifest as chevron patterns that point in the direction of crack initiation and are then clearly useful in the investigation of a failure. The image below shows the fracture of a hardened and tempered steel that had fractured due to forging defects located at the top right corner of the image. The fracture shows subtle ‘river marks’ radiating out from this corner.
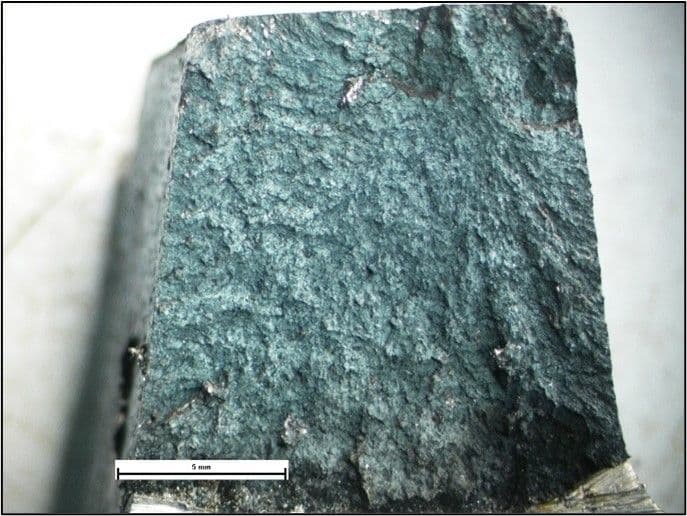
Below is another example of a hardened steel component that had fractured and again exhibiting chevron patterns, or ‘river marks’, indicating crack propagation was from right to left.
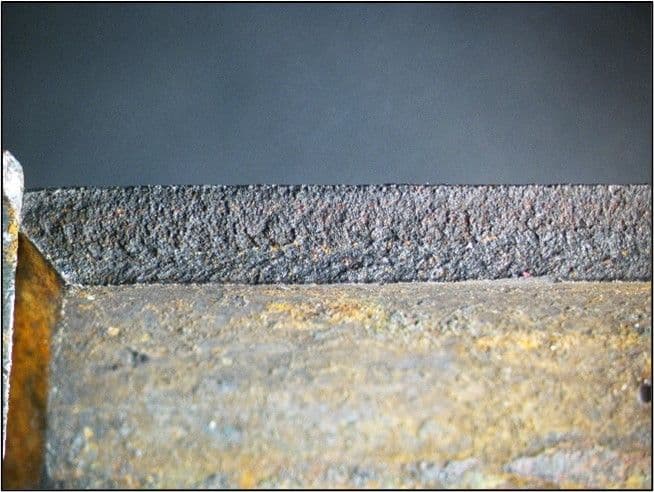
However, ‘river marks’ are not always observed, and a brittle fracture may be relatively devoid of any features from which to identify locations of initiation or crack propagation direction, as shown in the image below of a fracture in an aluminium alloy casting. On this occasion, severe deformation of the threads in the blind hole on the right indicated machining tolerances between the thread in the casting and the bolt were incorrect. This caused an ‘interference’ fit between the threads leading to the development of high hoop stress around the hole and the subsequent failure of the casting material.
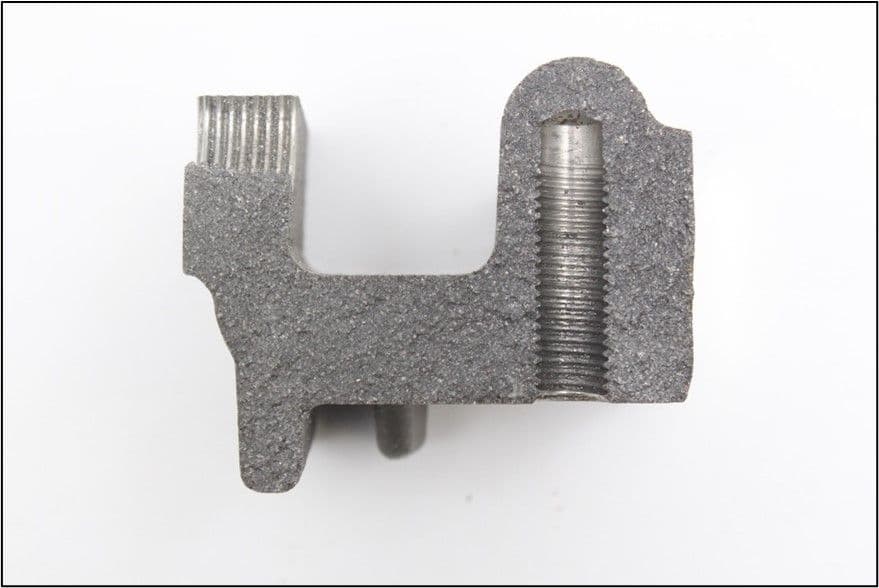
Avoiding
Some materials will always be inherently brittle and so measures should be taken to reduce the probability of fracture including;
- Minimising the presence of defects, such as voids in castings, or machining marks.
- Heat treatment and compositional changes to a material to increase fracture toughness and reduce notch sensitivity, and improve grain size.
- Stress relief to reduce residual stresses.
- Selection of materials (steels) that exhibit a ductile-brittle transition temperature appropriate for the use. Some steels may exhibit a sudden change in behaviour from ductile to brittle, and therefore could fail catastrophically if used below the critical temperatures. An often-cited example is the steel used in the construction of the RMS Titanic. The hull plates exhibited transition temperatures of between 32°C and 56°C, and the water temperature at the time was reported to be -2°C i.e. the materials were well below their transition temperature. The rivets used in the hull also exhibited brittle behaviour at the low temperature on the night of the accident, when they would ‘normally’ be expected to behave in a more ductile manner (there are many papers discussing the effects of the brittle behaviour of the hull plates and rivets on the sinking of the RMS Titanic). Correct composition and heat treatments may modify this transition temperature and may be identified by impact tests at a range of temperatures e.g. Charpy and Izod tests. Such tests can also identify how a material may respond to high strain rate loading.
- Avoidance of microstructures that are inherently brittle, such as martensite. Tempering the martensite can reduce brittleness but can be carried out to maintain sufficient strength for the application.